Articles
Driving your Company’s IoT ROI by linking it with Predictive Maintenance
Unlike the consumer sector, manufacturers have been using IoT for years. Properly focused IoT capabilities have driven huge change and ROI in manufacturing across a range of operational applications. However, in many instances, it has become a self-perpetuating data gathering exercise with no real focus. IoT is not an end in itself and needs to have clear business goal and ROI.
Linking your IoT to a practical application like Predictive Maintenance can drive significant ROI and put a clear structure on your IoT roadmap and measurement of success.
Predictive Maintenance (PdM): the use of Advanced Predictive Analytics and multiple historic data sources, aims to predict when and where an asset will fail (and why). This capability offers manufacturers the opportunity to reduce operating costs (10-25%) and product development costs (25%). The typical challenge for traditional manufacturers is that the older processes which are problematic gather little or no data and the newer equipment which gathers all data is relatively problem free.
Typical data points that need to be gathered for PdM include:
- Asset Data – Age, Product specifications, etc.
- Usage – Temperature, Oil Pressure, Load, Production Speeds, Voltage, Acoustics, Geographical – Physical Position.
- Maintenance logs – Date of last repair, unstructured data and repairs.
- Weather data – Temperature, humidity, rainfall, etc.
Low cost sensors have made data collection relatively cheap, however, not all data is required for all assets, and implementing an IoT strategy without focusing on what you want to achieve will end up in large quantities of irrelevant data.
In this blog, we’ll look at key factors that should be addressed when implementing an IoT and Predictive Maintenance strategy.
Key Challenges
Enterprise Wide
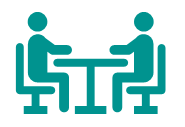
One of the first challenges is to stop your IoT or PdM strategies from becoming siloed. This is an enterprise capability that has multiple applications across the enterprise.
Both PdM and IoT offer potential for improving manufacturing’s performance in product quality, targeted maintenance, supply chain, warranty and customer satisfaction, so the planning must be done at a corporate level.
If the IoT or PdM is carried out in siloes and pockets of insufficiently digitalised processes, this will limit the manufacturer’s ability to get the right data and deploy the results across all the touchpoints where they are needed.
The IoT and PdM strategy is a truly cross functional collaborative effort and manufacturers need to bring together expertise from different teams to understand the real business requirements and the critical data and the practical outputs required to answer the objectives. The strategy may require new organisational skillsets such as data scientists to translate the business requirements into data mining objectives and understanding how the outputs can be deployed into the existing infrastructure.
Managing the Politics
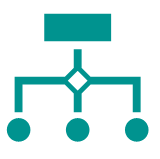
Ironically the most critical factor has nothing to do with technology or data. PdM will not be a full replacement of your existing maintenance programming but it will mean that the resource scheduling will change. This means you will need to navigate the political complexities of getting line-of-business, IT and Operational Technology to work together and to buy into the new way of scheduling your maintenance resources.
All the respective stake holders bring very important skill sets to the equation, but need governance and leadership.
Start with the End in Mind
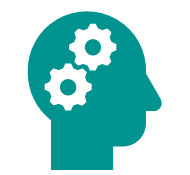
Looking at your critical assets, which ones are causing the most trouble, and what are the critical data sets you are missing? This will help focus the IoT on gathering the critical data at the appropriate level. Planning practical deployment of the analytical outputs will help map the business objectives, data gathering, data analytics and deployments based on desired outcomes of the business owners. Predictive Maintenance in many cases will only use your existing data, so the IoT strategy can start relatively small, focusing on key missing data that will improve your existing PdM data models delivering greater accuracy, insight and ROI. This will build momentum and buy in for the growing IoT strategy.
Prove the Value
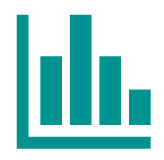
Predictive Maintenance Pilot projects should have three key ingredients for success:
- A problem area that is causing real pain – e.g. frequent unplanned downtime.
- Available and relevant data – Here, sensors and external weather data may need to be set up for several months to gather sufficient data.
- Ability of your operational systems to consume the outputs e.g. an alert that a specific asset is going to fail.
The long-term value of the IoT strategy will be determined based on the initial PdM pilots that prove their value. An example of this is a manufacturer who ran a 6 month project to improve the reliability and productivity of a specific rotating piece of equipment. IT held some of the data already (equipment usage, torque settings, energy consumption and maintenance logs), Additional IoT data was gathered onto a central platform (external temp., harmonics, oil temp.) to increase the accuracy and insights produced by the analytics. Outputs were embedded in the existing maintenance dashboards, alerting engineers when the asset started to behave in a way that indicated it was going to fail.
Conclusion
Manufacturers can significantly increase their operational efficiency and profitability by effectively taking advantage of IoT. To effectively do this takes a true collaboration across multiple divisions and skillsets and to focus clearly on an end goal.
Predictive Maintenance offers the ideal vehicle to prove the value and put a structured roadmap in place to enable manufacturers to build a credible IoT strategy that delivers short and long term ROI.
Version 1’s experienced consultants are on hand to help you understand your SPSS needs – from consultancy and training to finding the best software and license type for your analytical and usage requirements. Contact us to discuss your requirement and identify the best SPSS solution for you.
Related Articles
Take a look through our SPSS Articles covering a broad range of SPSS product and data analytics topics.