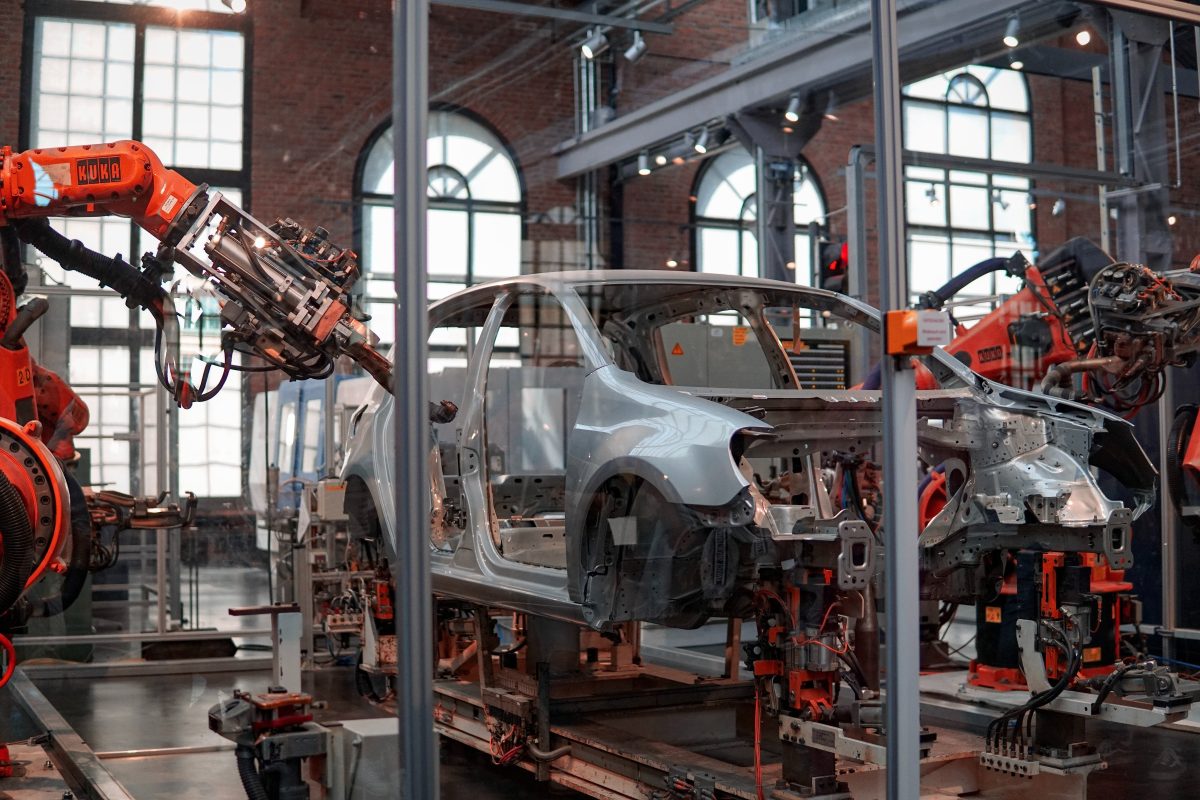
Predictive Analytics
for Manufacturing
Maximise utilisation and performance and minimize unscheduled downtime that can disrupt production, service and delivery.
In today’s fast paced market, manufacturing downtime and the release of substandard products can quickly damage your reputation and bottom line.
Version 1 helps asset-intensive organisations keep manufacturing processes, infrastructure and equipment running efficiently to maximise utilisation and performance and minimise costly, unscheduled downtime that can disrupt production, service and delivery.
Predictive Analytics for Manufacturing
Predictive modelling can assist organisations with keeping manufacturing processes, infrastructure and equipment running efficiently to maximise utilisation and performance and minimise costly, unscheduled downtime that can disrupt production, service and delivery.
Utilising Predictive maintenance allows companies to:
- Predict asset failure based on usage and wear characteristics
- Estimate and extend component life
- Increase return on assets, productivity and lifetime
- Optimise maintenance, inventory, and resource schedules
- Optimise assets for better availability, utilisation and performance
- Prevent Downtime
- Enhance operations and supply chain processes.
Primary Analytics Solutions for Manufacturing
Design the analytical solution that is best for your business.
Predictive Maintenance
Predictive maintenance differs considerably from the traditional approaches to determining when to service or replace equipment. Waiting until a component fails incurs lost production time and revenue. In-person inspections are expensive and purely based only on the inspector’s best guess. Following the manufacturer’s recommended maintenance schedule often results in replacing parts unnecessarily.
Benefits of Predictive Maintenance include:
- Predict asset failure based on usage and wear characteristics
- Estimate and extend component life
- Increase return on assets, productivity and lifetime
- Optimize maintenance, inventory, and resource schedules
- Optimise assets for better availability, utilisation and performance
- Prevent Downtime
- Enhance operations and supply chain processes
Predictive Quality
In-depth root cause analysis identifies the key factors of substandard batches so adjustments can be made to save the batch.
- Reduce Recalls / Warranty claims
- Reduce time to identify issues
- Enhance operations and supply chain processes
- Detect emerging quality problems and reliability issues early enough
- Avoid costly call backs and lost production
- Reduce scrap work, Inspections effort and Warranty claims
- Make adjustments to predictive maintenance schedules and corrective actions
- Maximise shipping rates cost-effectively
- Improve Brand Value and After Sales Support recommendations
Operational Efficiency
Innovative companies consistently look for ways to achieve their goals more efficiently, quickly respond to market changes and take advantage of emerging opportunities. Predictive Maintenance and Quality solutions can help your organisation continuously improve Operational Efficiency by optimizing existing processes and turning operational data into actionable insights.
Opportunities to improve operational efficiency, reduce operational costs and maximise productivity, exist in various operational areas, including:
- Workforce and Resources Scheduling
- Equipment and Spare-Parts Inventory
- Capital and Strategic Planning
- Supply Chain Management
- Building Management
- Energy Efficiency
- Facilities Management
Manufacturing Case Studies
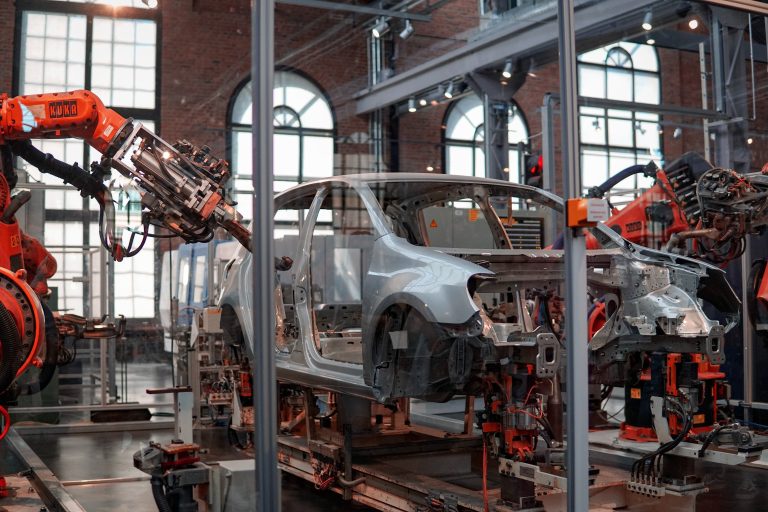
Case Study – Daimler Group
Daimler AG was looking for a way to maximize the number of flawlessly produced cylinder-heads by making targeted process adjustments. They also wanted to increase productivity and shorten the ramp-up phase of its manufacturing process. Using IBM SPSS software, Daimler is now able to analyse the plethora of data obtained in the production process and gain deep insights into the key factors that influence product quality.
Latest Resources from our Learning Hub
Industry-Leading Support to Make the Most of Your Advanced Analytics Software
Our Documentation & Support section provides 24/7 access to online fault logging as well as support documentation and FAQs.
Support Documentation
Support FAQs
Log A Support Ticket
Discover More Industry-Specific Solutions
Version 1’s SPSS experts can consult and deliver a wide variety of analytics solutions across a broad range of industry sectors. Find out more at the links below.